Precision and Innovation Drive the Future of CNC Machining
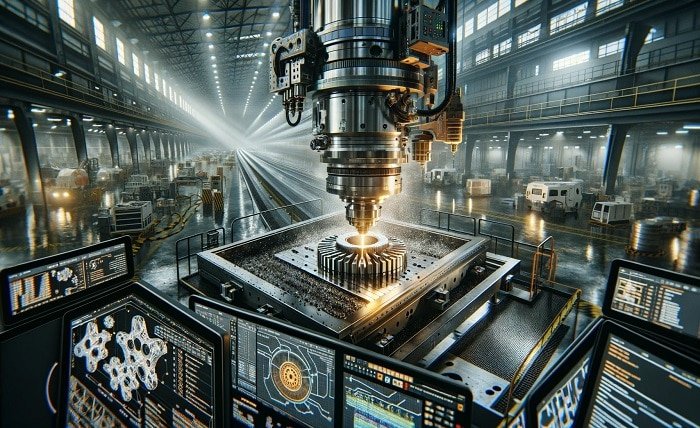
This blog post emphasizes the significance of precision and innovation in CNC machining amid today’s rapidly evolving tech landscape. It explores the evolution, technologies, applications, and future prospects of CNC machining, showcasing its capacity to enhance accuracy, efficiency, and repeatability in manufacturing.
The Evolution of CNC
The history of CNC machining is a testament to human ingenuity and the relentless pursuit of improvement. The concept of using numerical control for machining dates back to the mid-20th century. Initially, machines operated using punched tape, which encoded commands for machine movement. These early systems laid the groundwork for modern CNC, albeit with significant limitations in speed and complexity.
With the advent of digital computing, CNC technology took monumental strides forward. The introduction of direct numerical control (DNC) allowed multiple machines to be operated from a central computer, enhancing productivity and flexibility. Computer-aided design (CAD) and computer-aided manufacturing (CAM) software further propelled CNC’s capabilities, enabling more complex designs and efficient programming.
Today’s CNC machines are marvels of technology, integrating advanced software and hardware to deliver unparalleled performance. These machines can execute intricate operations with minimal human intervention, thanks to advancements in artificial intelligence and machine learning. The evolution of CNC continues, driven by the relentless pursuit of precision and innovation.
Key Technologies in CNC Machining
In the world of CNC machining, technological advancements are at the heart of innovation. The latest CNC tools and software have transformed the industry, enabling faster production, improved accuracy, and enhanced capabilities. One such advancement is the introduction of multi-axis machines, which offer greater versatility in creating complex parts.
Five-axis CNC machines, for instance, allow for simultaneous movement along multiple axes, reducing the need for multiple setups and increasing efficiency. This capability is particularly beneficial for industries like aerospace and automotive, where complex geometries are common. Manufacturers can produce intricate components with fewer errors and faster turnaround times.
Another key technology is the integration of Internet of Things (IoT) devices within CNC systems. IoT-enabled machines can communicate real-time data to operators and maintenance teams, facilitating predictive maintenance and minimizing downtime. This connectivity enhances the overall efficiency of manufacturing processes and provides valuable insights into machine performance.
Applications of CNC Machining
CNC machining finds applications across a wide range of industries, each benefiting from its precision and efficiency. In aerospace, CNC machines produce critical components like turbine blades and structural parts, where precision is paramount for safety and performance. The ability to manufacture these parts with tight tolerances ensures reliability in demanding environments.
The medical industry also relies heavily on CNC machining for producing implants, prosthetics, and surgical instruments. These products require exact specifications to ensure compatibility with the human body and functionality in medical procedures. CNC’s ability to deliver high precision and consistency is indispensable in meeting these requirements.
In the automotive sector, CNC machining is used to create engine components, transmission parts, intricate interior features, and spherical bearings. The demand for lightweight materials and complex designs in modern vehicles necessitates the capabilities of CNC machines. By streamlining production processes and improving part quality, CNC machining plays a vital role in the automotive supply chain.
Importance of Precision and Innovation in CNC
Precision and innovation are the cornerstones of CNC machining, driving both efficiency and quality in manufacturing processes. Precision ensures that parts meet exact specifications, reducing errors and rework. This accuracy is crucial in industries where even the slightest deviation can have significant consequences.
Innovation, on the other hand, fuels the development of new technologies and methodologies within CNC machining. The continuous quest for improvement leads to the creation of more advanced machines, software, and processes. This innovation not only enhances existing capabilities but also opens up new possibilities for industries to explore.
For manufacturers and engineers, the importance of precision and innovation cannot be overstated. By staying at the forefront of these principles, businesses can remain competitive in a rapidly changing landscape. This commitment to excellence fosters a culture of constant improvement and sets the stage for future success.
Conclusion
Now that we have explored the fundamentals, technologies, applications, and future of CNC machining, it is evident that this technology will continue to play a vital role in manufacturing. Its precision, efficiency, and versatility make it an invaluable asset for industries seeking to stay competitive in today’s market.